Custom Wafer Static Mixers
Custom Static Mixer
The patented Komax custom Wafer Static Mixer is designed to fit between existing pipe flanges of any specification. This makes the wafer-style static mixer easier for new and retrofit installations when there is limited space available and you are not able to install a traditional static mixer. In addition to solving the limited space availability, the Komax Wafer Static Mixer offers advantages over conventional static mixers by allowing up to three injection ports and utilizing patented vortex-generating element technology with clog-resistant counter-flow injection. Designed to clamp between pipe flanges Komax Wafer Mixer technology employs a unique vortex-generating element (see image group1) that helps achieve a desirable mixing quality by creating three-way counter-rotating vortex pairs as compared to typical energy-inefficient two-way mixers on the market. The element height and inclination angle offer short mixing length with low-pressure loss in various flow conditions. The additive chemical is introduced in the center line of the wafer static mixer on the upstream side. A discharge cone (see image group 2) enables the injected chemical to be distributed evenly through the three vortex-inducing passages. The pressure difference between the front and backside of each element produces a reversed flow that carries the chemical back toward the rear side of the mixer. Intensive mixing occurs by the resulting vorticial structure from the distinctive three-way counter-rotating vortex pairs.
Industries
Typical Applications
- Water Flocculation
- sodium hypo
- chlorine & alum
- chemicals
- water
- polymer solution
- aq chemicals
- sodium hydroxide
- dilute ACH
- chlorine
- sulfuric acid
- sodium hypochlorite
- pH Control
- dechlorination
- chloramination
- Mixing any other additive into water


Product Benefits
Non-clogging (Hi-Pass) Mixing Elements
Hydraulic forces generated by the patented hi-pass mixing elements disperse the centerline injected chemical across the pipe ID, thereby providing high degree of dispersion and mixing.
Technical Specifications and Available Options for Wafer Static Mixers
Sizes are available from 4” to 60” nominal diameter and in standard materials of construction: Carbon Steel, Stainless Steel, PVC, FRP, and can also be made from Titanium or specialty metal alloys as required.
End Connections & Available Custom Options
- Flanged Ends: N/A
- Threaded Ends: N/A
- Injection Ports: Additive injection connections are offered in male or female NPT or flanged end connections as required by the customer.
- Injection Quill: An injection port or quill can be added to the static mixer to allow for an additive stream to be injected directly into the static mixer with desired connection type (NPT, Flanged, Socket Weld, etc).
Available Materials and Sizes
- Diameter: 4″ – 60″
- Material: Carbon Steel, Stainless Steel, PVC, FRP, Specialty Alloys/Exotic Materials
Wafer Mixer Sizing Table
Wafer Line | Sch. STD Pipe ID | Connecting flange Raised Face Dia. | |||||||||||||||
Size | (inch) | (inch) | |||||||||||||||
4″ | 4.026 | 6.19 | |||||||||||||||
6″ | 6.06 | 8.5 | |||||||||||||||
8″ | 7.98 | 10.62 | |||||||||||||||
10″ | 10.02 | 12.75 | |||||||||||||||
12″ | 12 | 15 | |||||||||||||||
14″ | 13.25 | 16.25 | |||||||||||||||
16″ | 15.25 | 18.5 | |||||||||||||||
18″ | 17.25 | 21 | |||||||||||||||
20″ | 19.25 | 23 | |||||||||||||||
24″ | 23.25 | 27.25 | |||||||||||||||
* One or multiple injection ports can be provided | |||||||||||||||||
*Line Sizes bigger than 24″ are also available upon request | |||||||||||||||||
* Available in Carbon steel, Stainless Steel, FRP, PVC, CPVC and alloys etc | |||||||||||||||||
* Typical wafer mixer thickness/ length is 2″ |
Additional Product Details
If your questions about our products are not answered here, get in touch with us for more information.
See ALl FAQsOur Custom Product Process
Getting a Komax Systems product for your industrial process is simple! To get started, get in contact with us! Give us a call or submit a quote via our website to get your quote started.
Once we receive your request and the information associated with your process one of our sales engineers will reach out to make sure we've got all of the information needed to properly develop your quote. With all the correct information, our sales engineers can populate a unique quote specific to your custom design and your process' needs. Once the quote is finalized it is then paired with a drawing mock-up of your unit to make sure the specifications are to your liking and perfect for your system.
As soon as the quote and drawing are approved your unit is then off to fabrication. While your unit is being manufactured you are kept up to date on its progress and you will be notified once your new Komax Systems product is on its way to you!
Submit Your Request
Fill our out easy online form and get in touch with us!
Talk With Our Experts & Get a Quote!
Our experts will fine tune your quote to meet your projects specifications.
Get a Custom Design of Your Product
Get a sense of what your product will look like and how it will fit into your system.
Fabrication and Shipment of Your Order
Once approved we have the unit manufactured and shipped off to you!
Related Case Studies or Products
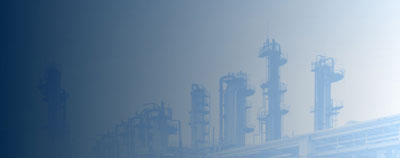
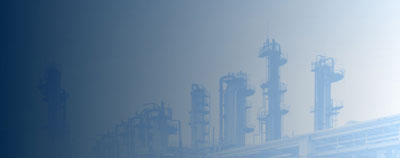
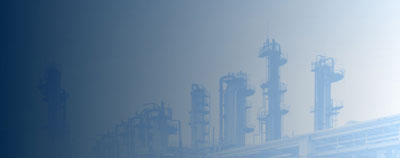